The type of diamond grit used in diamond saw blades and the bonding matrix are crucial factors that influence the performance, cutting efficiency, and durability of the blades. Here's an overview of these components:
Diamond Grit:
Natural Diamond or Synthetic Diamond: Diamond saw blades can use either natural or synthetic diamonds. Synthetic diamonds are often preferred for their consistency and controlled quality.
Grit Size: The diamond grit size refers to the size of the individual diamond particles on the blade. Grit sizes vary, and the choice depends on the material being cut. Coarser grits are suitable for softer materials, while finer grits are used for harder materials.
Diamond Shape: The shape of the diamond particles can vary, including round, cube, and irregular shapes. The choice of diamond shape can affect cutting efficiency and the ability to grind through materials.
Coating: Some diamond grits may have coatings such as nickel or other metals to enhance bonding with the matrix and improve overall performance.
Bonding Matrix:
Metal Bond, Resin Bond, or Hybrid Bond: The bonding matrix holds the diamond grit in place and affects how the diamonds interact with the material being cut. There are different types of bonding matrices, including metal bond, resin bond, and hybrid bond.
Metal Bond: Metal bonds are typically composed of various metals like cobalt, bronze, or other alloys. Metal bond saw blades are known for their durability and are suitable for cutting hard and abrasive materials.
Resin Bond: Resin bonds are made from a mixture of resin and powdered metal. Resin bond saw blades are known for providing a smooth finish and are often used for cutting softer materials.
Hybrid Bond: Hybrid bonds combine elements of both metal and resin bonds, offering a balance of durability and precision. They are suitable for a wide range of applications.
Vitrified Bond: In some cases, a vitrified bond, which involves using a glass-like matrix, is used. Vitrified bonds offer excellent resistance to heat and are suitable for high-temperature applications.
Segmented Design: The bonding matrix is often segmented into sections on the blade. This segmented design allows for better cooling, debris removal, and improved cutting performance.
Contributions to Performance:
Wear Resistance: The bonding matrix contributes to the wear resistance of the blade. A well-designed bonding matrix helps retain the diamond grit and prevents premature wear.
Cooling and Chip Removal: The bonding matrix affects the ability of the blade to dissipate heat generated during cutting. It also plays a role in facilitating the removal of chips and debris from the cutting area.
Cutting Speed: The bonding matrix influences the cutting speed of the blade. A proper balance between the hardness of the matrix and the abrasive nature of the diamond grit is crucial for achieving optimal cutting efficiency.
Precision and Finish: Different bonding matrices provide varying levels of precision and surface finish. Resin bonds, for example, are known for delivering smoother finishes, while metal bonds excel in applications where durability is paramount.
Material Compatibility: The choice of bonding matrix is often tailored to the specific material being cut. Certain matrices may be better suited for cutting concrete, while others are more effective for cutting granite or asphalt.
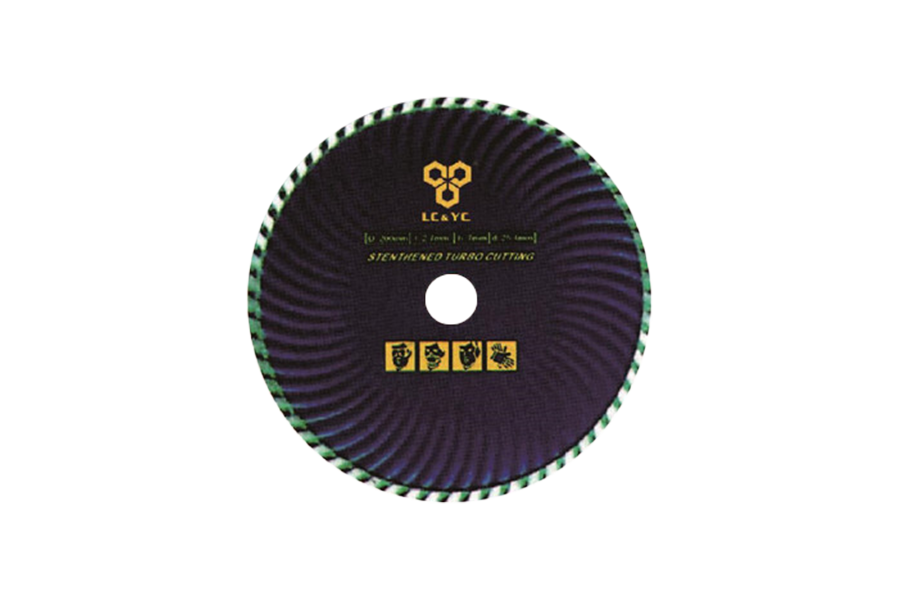